Choosing a plastic molding company with the right experience is key to ensuring your product meets its intended specifications. There are 5 different types of injection molding, each with unique advantages and applications.
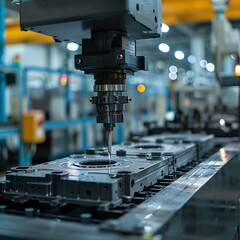
A molten plastic mixture is forced under high pressure into a custom-made mold to take the shape of the finished part. The molding process uses a range of guiding components, including ejector pins and lifters to ensure damage-free removal of the part. Read on Florida Plastic Mold Manufacturer for more details.
Plastic injection molding is a method that allows for precise control of the shape, size, and thickness of the plastic. This makes it a popular choice for businesses that require accurate, high-quality products. This process can be used for a variety of applications, from automotive to medical. It is also a great option for creating large, hollow parts, such as road cones and storage tanks. Injection molding is highly efficient, making it an economical and environmentally friendly option for producing high-quality products.
Precision in plastic injection molding depends on several factors, including the design of the mold and the use of high-quality materials. The accuracy of the mold is also dependent on the type of plastic resins used in the manufacturing process, as well as the dimensional tolerances of the product. It is important to ensure that the molded part will fit the final product before production begins. This is accomplished by implementing strict process control measures, such as monitoring temperature, pressure, and cycle time.
A quality plastic injection molding manufacturer should utilize advanced techniques to achieve the highest level of precision. These include using high-speed milling, slow wire EDM, and mirror EDM to ensure that the finished product will be smooth and accurate. These methods also help to prevent defects, such as flash, and increase the longevity of the mold. In addition, precision segmented control of injection and holding pressure is an essential technology for precision injection molding.
Injection mold manufacturers need to have a comprehensive understanding of the capabilities of their machines and the capabilities of their staff in order to produce consistent, high-quality results. This is especially critical for precision injection molding, which requires a deep understanding of the material behavior and machine capabilities. It is also important to ensure that the product meets the exact specifications and tolerances required by the customer.
A company that specializes in precision injection molding can provide their customers with a range of benefits, including cost savings and reduced cycle times. This process is ideal for a wide range of industries, including automotive, medical, and aerospace. These companies can benefit from a partnership with a plastic injection molding company that offers flexible pricing options and just-in-time inventory strategies.
Flexibility
Plastic injection molding is a highly flexible process that allows manufacturers to produce a variety of products. It can even be used to manufacture complex parts with intricate features, allowing them to meet the specific needs of designers and engineers.
This method of producing plastic parts requires fewer tools than other methods and produces less scrap. It also uses a lower amount of energy, making it a greener option for manufacturing plastics. Plastic injection molding also offers excellent flexibility in terms of materials, which can be modified to suit the product’s requirements. The versatility of this process allows for a higher level of customization and reduces the need for additional assembly work, resulting in cost savings for the customer.
The flexible nature of injection molding makes it an ideal choice for companies with limited budgets or high-volume orders. The initial investment in the mold is quickly offset by the low cost per unit. In addition, this method is compatible with a wide range of different types of plastics. This gives manufacturers greater flexibility when designing and creating products, enabling them to choose the best material for each application.
During the injection molding process, the raw material is fed into a barrel with a reciprocating screw that mixes and homogenizes the thermal and viscous distribution of the polymer. The screw also mechanically shears the polymer to further reduce its viscosity. This allows the polymer to be injected into a mould with a much lower pressure than other molding methods.
Injection molding is a fast and reliable method for producing large quantities of plastic parts. It is also a great choice for creating a complex shape, and it can accommodate varying design features without increasing the production time. The flexibility of this process makes it a popular choice for many industries, including aerospace and medical applications.
The main drawback of plastic injection molding is the upfront costs involved in designing and manufacturing a custom mold. However, the overall cost of injection molding decreases as the production quantity increases. This type of plastic molding is often preferred for long-term and high-volume manufacturing projects, as the production rate can justify the upfront cost.
Efficiency
The production of plastic parts is a complex process that requires precise control to ensure the best results. To ensure this, you need to work with a company that specializes in the manufacture of injection molds. Choosing a specialist in mold manufacturing can save you time and money in the long run. They will know how to make your project as efficient as possible so that it meets industry standards and stays within budget.
Injection molding is an effective and economical method for producing parts that are used in a wide range of applications. The process is able to produce large quantities of parts in a short amount of time, which can be beneficial for your business. It also helps reduce your overall costs by minimizing waste and scrap.
Plastic injection molding is a versatile process that can be used with many different materials. In fact, it is one of the most common methods for creating products made from polymers. It can be used to create almost any kind of product, from toys to medical devices. It can even be used to make multiple parts of the same product, such as a toothbrush with a soft grip or hard base.
The first step in the injection molding process is to design a product. This is done using a computer-aided design (CAD) program. Once the design has been completed, it is ready for production. The CAD file is sent to a manufacturer, who creates the actual mold, or tool. The mold is usually made of aluminum or steel and has a cavity in the shape of the product. It also has a sprue to introduce the molten plastic, a runner system to lead it to the cavities, and gates to enter the individual cavities.
It is important to choose the right plastic for your product. This will help determine the strength and durability of the part. In addition, the material must be able to withstand the required environmental conditions and temperature. There are many different types of polymers that can be used for injection molding, including thermoplastics, thermosets, and elastomers.
Reliability
Plastic injection molding is a remarkable technology that allows manufacturers to create intricate components with unmatched efficiency. However, it isn’t without its challenges. Various factors can lead to mold failure, and when they do, engineering failure analysis becomes essential in uncovering the root cause of these issues. This process is crucial to ensure that products are designed and manufactured correctly, and have the chance to live up to expectations on the market.
One of the most common causes of plastic mold failure is high wear and tear due to poor quality material selection and design. These issues can also arise from environmental factors like temperature variations and humidity levels. Another important factor is the type of resin used. High-performing and specialty resins typically come with a higher cost, but they also offer greater durability and strength.
Proper maintenance and adherence to injection molding quality standards are also vital to extending the lifespan of plastic molds. This includes periodic cleaning and maintenance of the mold, as well as a consistent record of services that have been performed on it. These records can help identify potential problems and sources of error that may occur in the future, saving both time and money.
Injection molds must be able to withstand the high temperatures and pressures involved in the production process. When these conditions aren’t met, the plastic can burn or deform in ways that compromise the product’s integrity. In addition to the impact on product quality, these conditions can increase production costs and require more frequent repair and maintenance.
To avoid these issues, engineers can use DOE to assess the reliability of their plastic injection molds. This tool helps them understand the flow and cooling processes of plastic in the mold, and predict and solve potential problems such as sink marks and flow lines. This can improve mold design and quality, and reduce the amount of maintenance required to keep it running efficiently.
Other factors that affect injection mold durability include the injection mold temperature, speed, and pressure, as well as the structure of the mold itself. For example, a study conducted at a manufacturing facility using glass-filled polymers found that injecting them with less pressure and moderating the injection mold temperature helped extend their lifespans by 15%, and enabled them to meet project specifications.