Pianos are one of the most difficult items to move, and even the slightest damage can have disastrous consequences. With the help of a team of skilled movers and careful preparation, however, you can minimize the risk of complications and have a stress-free relocation.
Start by measuring the dimensions of every doorway, hallway, and staircase. This helps Piano Movers Denver plan their route and navigate obstacles, especially in homes with limited doorways or steep stairs.
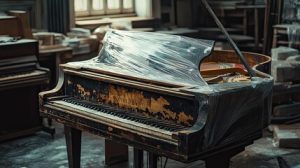
Ensure Proper Protection
The key to a stress-free piano move is meticulous preparation. This involves assessing the piano and moving environment, gathering specialized supplies, and enlisting help. A professional mover has the tools to safely transport a large, delicate instrument without risking damage or injury.
These tools include a padded piano dolly that supports the weight of the instrument and makes maneuvering it through tight spaces more manageable. They also use padded covers to protect the instrument’s surfaces from scratches and dents during transport.
Additionally, they ensure their team members have proper equipment to safely lift the piano and avoid injury. This includes work gloves to improve grip, corner protectors to prevent strap damage, and a well-thought-out moving path that accounts for obstacles like stairs and tight doorways. The team should also have an assigned leader to communicate and coordinate with each other. Finally, movers should use the correct lifting technique—bend at the knees and keep their backs straight—to reduce strain on their muscles.
Hire Professional Movers
Professional movers have the skills and equipment to move your piano safely. Although they may cost more than your typical moving company, their expertise can save you from costly repairs that could occur when you attempt to move your piano without help.
When choosing a piano moving company, ask for references from previous clients. Honest movers are proud to share these references and will be happy to connect you with satisfied customers.
Before the move day, measure the dimensions of your home’s doors and staircases. This information will help the movers prepare for any difficulties that may arise during the process. Communicating these details clearly with the movers will help prevent misunderstandings and foster a positive and collaborative environment. You can also minimize external stressors by arranging the move for a day with minimal traffic and weather conditions. This will make the process more efficient and reduce the risk of damage to your piano or other belongings.
Obtain Insurance Coverage
In addition to proper preparation, obtaining insurance coverage can help alleviate any stress caused by potential damage during the move. When assessing insurance options, look for policies that specifically include piano moving and transportation. Additionally, make sure that any pre-existing damage is covered by the policy before it’s put in effect.
Having a detailed piano appraisal can also be beneficial when it comes to determining the right insurance coverage. Moreover, a professional appraisal can help you determine the true value of your instrument and can come in handy in a variety of situations, including selling, replacing, or passing it down to future generations.
Obtaining the right insurance policy can protect your investment and help you avoid any costly repairs or replacements after the move is complete. Be sure to discuss your coverage options with your movers and gather all relevant documentation before the move.
Pack Your Piano Carefully
The hefty weight and delicate internal components of pianos present unique moving challenges. Hiring professional movers, obtaining insurance coverage, and taking appropriate precautions can make the relocation process stress-free.
To reduce the risk of damage to your piano, carefully pack it before the move. Use thick blankets and heavy-duty tape to safeguard your instrument from scratches and dents. This will also prevent other items from shifting during transit.
Before moving day, walk through your piano’s route with a friend and note any potential obstacles. Be sure to measure doorways, hallways, and staircases for clearance. You may need to temporarily remove doors or apply a special ramp for the piano. This preparation will help ensure that the piano and all other belongings arrive at their new home safely and in good condition. Moreover, it will also minimize the cost of extra labor. Assign clear responsibilities to all friends involved in the move to avoid any confusion.
Assign Clear Responsibilities
The success of a piano move depends on a variety of factors. Having clear responsibilities and open lines of communication with your professional movers is one way to guarantee a stress-free relocation experience. Provide them with a detailed description of the instrument and its specifications, as well as any potential obstacles that may arise along the move route. You can also specify the precise placement of the piano at its new location.
To avoid any confusion or misunderstandings, it is also crucial to select friends who are willing and physically capable of moving your piano. A trustworthy and reliable team can help ensure that the move goes smoothly, preventing injuries or damage. Moreover, choosing a time when traffic and weather conditions are minimal can minimize external stressors and reduce the risk of delays or complications. After the piano reaches its destination, give it time to acclimate to its new environment and schedule a professional tuning session.
Set Aside Emergency Funds
Whether you own an heirloom grand piano or a sturdy upright, moving it is no simple task. It requires specialized equipment and experience to prevent damage to the instrument and your home. Hiring professional movers reduces the risk of costly mistakes.
Before the move, remove all removable parts like the music stand and pedals, and secure them. Then, place the piano on a dolly that can support its weight and use heavy-duty straps to anchor it in place during transportation. This prevents the piano from jolting or slipping during transit and protects its delicate inner mechanics.
It is also wise to clear a path between the piano and its destination, as well as remove any obstacles or furniture that might hinder the movement process. Preparing the route and communicating it to movers in advance can help avoid surprises on the day of the move.